Table of contents
Yoke type roller bearing track rollers, stud type roller bearing track rollers
- Bearing design
- Load carrying capacity
- Angular misalignment
- Lubrication
- Sealing
- Speeds
- Noise
- Temperature range
- Cages
- Internal clearance
- Dimensions, tolerances
- Suffixes
- Structure of bearing designation
- Dimensioning
- Minimum load
- Design of bearing arrangements
- Mounting and dismounting
- Legal notice regarding data freshness
- Further information
Track rollers
Yoke type roller bearing track rollers, stud type roller bearing track rollers
Yoke and stud type roller bearing track rollers:
- are ready-to-fit needle or cylindrical roller bearings of single or double row design ➤ Figure to ➤ Figure
- are mounted on shafts or studs (yoke type track rollers) or supplied with a heavy-section roller stud with fixing thread and a mounting aid (stud type track rollers) ➤ Figure
- have particularly thick-walled outer rings with a crowned outside surface ➤ section
- can support high radial loads ➤ section
- tolerate axial loads which are due to small misalignment defects, skewed running or temporary contact running impacts ➤ section
- are available with or without an inner ring (yoke type track rollers)
- are produced with or without axial guidance of the outer ring (stud type track rollers are always produced with axial guidance)
- are open or sealed on both sides ➤ section
- are not mounted in a housing bore, but are supported on a flat mating track ➤ Figure
- can be adjusted to the mating track in the design with the eccentric collar, thus permitting, for example, larger manufacturing tolerances in the adjacent construction
Double row stud type track roller supported on a flat mating track
|
![]() |
Bearing design
Design variants
This range of yoke type track rollers comprises bearings:
- with or without an inner ring (without axial guidance) ➤ Figure, ➤ Figure
- with an inner ring (with axial guidance)
- Without eccentric collar
- With eccentric collar
Yoke type track rollers (general)
The bearings have thick‑walled outer rings and are mounted on shafts or studs
Yoke type track rollers are single or double row units mounted on shafts or studs ➤ Figure to ➤ Figure. They comprise thick-walled outer rings with a profiled outside surface and needle roller and cage assemblies or full complement needle roller or cylindrical roller sets. Yoke type track rollers can support high radial loads as well as axial loads arising from slight misalignment and skewed running. The bearings are available with or without an inner ring, with or without axial guidance and in sealed or open versions.
Typical applications
Proven areas of application of these products include cam gears, bed ways, conveying equipment and linear guidance systems.
Outside surface profile of the outer ring
The outside surface is predominantly crowned
Bearings with a crowned outside surface are predominantly used in practice since skewing usually occurs relative to the mating track and edge stresses must be avoided.
Radius of curvature
The radius of curvature of the outside surface is R = 500 mm. In the case of series NNTR..-2ZL, the radius is indicated in the product table.
Optimised INA profile
Yoke type track rollers NATR..-PP, NATV..-PP, NUTR and PWTR..-2RS have an outside surface with the optimised INA profile ➤ link. In yoke type track rollers with this curvature profile:
- the Hertzian pressure is lower ➤ Figure, ➤ Figure
- edge loading under tilting is lower ➤ Figure
- wear of the mating track is reduced ➤ Figure, ➤ Figure
- the operating life of the mating track is extended ➤ Figure
- the rigidity in the outer ring contact is increased ➤ Figure
X-life premium quality
Series PWTR is supplied as an X-life design. Due to a modified material and the optimised raceway geometry of the outer rings, the basic rating life has been increased by up to 30%. The static and dynamic load carrying capacity has also been increased. At the same time, the stress placed on the mating track has been reduced as a result of the optimised lateral surface profile and its improved surface quality.
Lower operating costs, higher machine availability
In conclusion, these advantages improve the overall cost-efficiency of the bearing position significantly and thus bring about a sustainable increase in the efficiency of the machine and equipment.
Suffix XL
X-life yoke type track rollers include the suffix XL in the designation.
Yoke type track rollers without inner ring, without axial guidance
The raceway must be designed as a rolling bearing raceway
Yoke type track rollers RSTO and RNA22..-2RSR do not have an inner ring ➤ Figure. Depending on the design, yoke type track rollers are also available as sealed versions ➤ section. They are particularly compact but require a hardened and ground raceway on the shaft or stud. Series RSTO is not self-retaining, which means that the outer ring and the needle roller and cage assembly can be fitted independently of each other. This gives simplified mounting of the bearings.
The rolling elements are guided by the cage. These designs do not have axial guidance of the outer ring. Axial guidance of the outer ring and needle roller and cage assembly (for RSTO only) must be provided in the adjacent construction.
Yoke type track rollers without inner ring, without axial guidance, open or sealed on both sides Fr = radial load Fa = axial load
|
![]() |
Yoke type track rollers with inner ring, without axial guidance
Yoke type track rollers STO and NA22..-2RSR have an inner ring ➤ Figure. Depending on the design, yoke type track rollers are also available as sealed versions ➤ section. Bearings with an inner ring are used if the shaft or stud does not have a hardened and ground raceway. Series STO is not self-retaining. This means that the outer ring, needle roller and cage assembly and the inner ring can be fitted independently of each other. This gives simplified mounting of the bearings.
The rolling elements are guided by the cage. These designs do not have axial guidance of the outer ring. Axial guidance of the outer ring and needle roller and cage assembly (for STO only) must be provided in the adjacent construction.
Yoke type track rollers with inner ring, without axial guidance, open or sealed on both sides Fr = radial load Fa = axial load
|
![]() |
Yoke type track rollers with inner ring, with axial guidance
Yoke type track rollers with an inner ring are used if the shaft or stud does not have a hardened and ground raceway.
Designs
The series NATR and NATR..-PP have a cage ➤ Figure. The series NATV and NATV..-PP have a full complement needle roller set, while yoke type track rollers NUTR have a full complement cylindrical roller set ➤ Figure and ➤ Figure. Yoke type track rollers PWTR..-2RS and NNTR..-2ZL have a full complement cylindrical roller set and a central rib ➤ Figure. Depending on the design, yoke type track rollers are also available as sealed versions ➤ section.
Bearings without a cage have the largest possible number of rolling elements and therefore have particularly high load carrying capacity. Due to the kinematic conditions, however, the speeds achievable with these bearings are somewhat lower than those achievable with the cage-guided yoke type track rollers.
Axial guidance of outer ring
The type of guidance is dependent on the series
In NATR and NATV, axial guidance is provided directly by contact washers, while in NATR..-PP and NATV..-PP this is provided by contact washers and plastic axial plain washers. In NUTR, the outer ring is guided by the rolling elements, in PWTR..-2RS and NNTR..-2ZL it is guided by the central rib and the rolling elements.
Corrosion protection
Corrosion protection by Corrotect
Series PWTR..-2RS-RR is protected against corrosion by the special Cr(VI)‑free coating Corrotect ➤ link. These bearings have the suffix RR.
Yoke type track rollers with cage, with axial guidance, open or sealed on both sides Fr = radial load Fa = axial load
|
![]() |
Yoke type track rollers with inner ring, full complement needle roller set, with axial guidance, open or sealed on both sides Fr = radial load Fa = axial load
|
![]() |
Yoke type track roller with inner ring, full complement cylindrical roller set, with axial guidance, sealed on both sides Fr = radial load Fa = axial load
|
![]() |
Yoke type track rollers with inner ring, full complement cylindrical roller set, with axial guidance, sealed on both sides Fr = radial load Fa = axial load
|
![]() |
Stud type track rollers (general)
The bearings have thick‑walled outer rings and a heavy-section roller stud
Stud type track rollers are similar in their construction to single and double row yoke type track rollers with axial guidance, except that the raceway is formed by a heavy-section roller stud with a fixing thread and type-dependent mounting aid, and with a type-dependent relubrication facility. Due to the thick-walled outer ring with profiled outside surface and the rolling element set, they can support high radial loads as well as axial loads arising from slight misalignment and skewed running. The stud type track rollers are available with or without an eccentric collar ➤ Figure to ➤ Figure.
Typical applications
Proven areas of application of these products include cam gears, bed ways, conveying equipment and linear guidance systems.
Outside surface profile of the outer ring
The outside surface is crowned
Stud type track rollers with a crowned outside surface are predominantly used since skewing usually occurs relative to the mating track and edge stresses must be avoided.
Radius of curvature
In series KR, the radius of curvature is R = 500 mm. The series KR..-PP, KRE..-PP, KRV..-PP, NUKR, NUKRE, PWKR..-2RS and PWKRE..-2RS have an outside surface with the optimised INA profile.
Optimised INA profile
In stud type track rollers with the optimised INA profile:
- the Hertzian pressure is lower ➤ Figure, ➤ Figure
- edge loading under tilting is lower ➤ Figure
- wear of the mating track is reduced ➤ Figure, ➤ Figure
- the operating life of the mating track is extended ➤ Figure
- the rigidity in the outer ring contact is increased ➤ Figure
X-life premium quality
Stud type track rollers PWKR(E) are supplied in the X-life design. Due to a modified material and the optimised raceway geometry of the outer rings, the basic rating life has been increased by up to 30%. The static and dynamic load carrying capacity has also been increased. At the same time, the stress placed on the mating track has been reduced as a result of the optimised lateral surface profile and its improved surface quality.
Lower operating costs, higher machine availability
In conclusion, these advantages improve the overall cost-efficiency of the bearing position significantly and thus bring about a sustainable increase in the efficiency of the machine and equipment.
Suffix XL
X-life stud type track rollers include the suffix XL in the designation.
Stud type track rollers without eccentric collar
Stud type track rollers without an eccentric collar do not have a defined adjustment facility in relation to the mating track on the adjacent construction in mounting of the bearings.
Designs
The series KR and KR..-PP have a cage, the design KRV..-PP has a full complement needle roller set. Series NUKR has a full complement cylindrical roller set, series PWKR..-2RS has a full complement cylindrical roller set and a central rib ➤ Figure to ➤ Figure.
Bearings without a cage have the largest possible number of rolling elements and therefore have particularly high load carrying capacity. Due to the kinematic conditions, however, the speeds achievable with these bearings are somewhat lower than those achievable with the cage-guided stud type track rollers.
Axial guidance of outer ring
The type of guidance is dependent on the series
In KR, axial guidance is provided directly by the contact flange and contact washer, while in KR..-PP and KRV..-PP this is provided by plastic axial plain washers, the contact flange and contact washer ➤ Figure and ➤ Figure. The outer rings of series NUKR and PWKR..-2RS are guided by the rolling elements and ribs ➤ Figure and ➤ Figure.
Relubrication facility
Stud type track rollers KR16 and KR19 with a hexagonal socket cannot be lubricated, while stud type track rollers KR16 and KR19 with a mounting slot have a relubrication facility.
Corrosion protection
Corrosion protection by Corrotect
Series PWKR(E)..-2RS-RR is protected against corrosion by the special Cr(VI)-free coating Corrotect ➤ link. These bearings have the suffix RR.
Stud type track roller without eccentric collar, with cage, sealed on both sides Fr = radial load Fa = axial load
|
![]() |
Stud type track roller without eccentric collar, full complement needle roller set, sealed on both sides Fr = radial load Fa = axial load
|
![]() |
Stud type track roller without eccentric collar, full complement cylindrical roller set, sealed on both sides Fr = radial load Fa = axial load
|
![]() |
Stud type track roller without eccentric collar, full complement cylindrical roller set, with central rib, sealed on both sides Fr = radial load Fa = axial load
|
![]() |
Stud type track rollers with eccentric collar
The bearings have a defined adjustment facility relative to the mating track
Designs with an eccentric collar can be adjusted by means of a hexagonal socket on the flanged or threaded side of the roller stud. The outer ring outside surface can thus be adjusted against the mating track. As a result, larger manufacturing tolerances can be tolerated in the adjacent construction. Furthermore, this gives improved load distribution when using several stud type track rollers and also allows preloaded linear systems to be easily realised.
Highest point of the eccentric collar
The highest point of the eccentric collar is indicated on the roller stud side, the eccentricity e is stated in the product tables. This is also the location of the radial relubrication holes, which should lie in the unloaded zone of the rolling contact.
Designs
Series KRE..-PP has a cage, NUKRE and PWKRE..-2RS have a full complement cylindrical roller set ➤ Figure to ➤ Figure.
Bearings with a full complement cylindrical roller set have the largest possible number of rolling elements and therefore have particularly high load carrying capacity. Due to the kinematic conditions, however, the speeds achievable with these bearings are somewhat lower than those achievable with the cage-guided stud type track rollers.
Axial guidance of outer ring
The type of guidance is dependent on the series
In the series KRE..-PP, axial guidance is provided by the plastic axial plain washers, contact flange and contact washers. In NUKRE, the outer ring is guided axially by the rolling elements, in PWKRE axial guidance of the outer ring is provided by the central rib and rolling elements.
Stud type track roller with eccentric collar, with cage, sealed on both sides Fr = radial load Fa = axial load
|
![]() |
Stud type track roller with eccentric collar, full complement cylindrical roller set, sealed on both sides Fr = radial load Fa = axial load
|
![]() |
Stud type track roller with eccentric collar, full complement cylindrical roller set, with central rib, sealed on both sides Fr = radial load Fa = axial load
|
![]() |
Optimised INA profile
Advantages
The advantages of the optimised INA profile are:
- lower Hertzian pressure under tilting ➤ Figure and ➤ Figure
- higher basic rating life of the outer ring and mating track ➤ Figure
- reduced wear between the outer ring outside surface and the mating track ➤ Figure and ➤ Figure
- increased rigidity in the outer ring contact ➤ Figure
Hertzian pressure curve
Optimised INA profile, profile R = 500, cylindrical profile
The Hertzian pressure curve is more favourable for bearings with an optimised INA profile than for bearings with a cylindrical profile or with a profile where R = 500 mm (load Cr w/Pr = 5) ➤ Figure.
Hertzian pressure curve
|
![]() |
Maximum Hertzian pressure
Reduced Hertzian pressure with optimised INA profile
The maximum Hertzian pressure is significantly lower for bearings with an optimised INA profile than for bearings with a cylindrical profile or with the profile R = 500 mm ➤ Figure.
Maximum Hertzian pressure, stud type track roller NUKR80, Fr = 13 800 N (Cr w/Pr = 5) pH = Maximum Hertzian pressure β = tilt angle
|
![]() |
Basic rating life of mating track
Longer rating life of mating track
The rating life of the mating track is significantly longer for outer rings with an optimised INA profile than for bearings with the profile R = 500 mm ➤ Figure. Yoke type track rollers NUTR15 ➤ Figure were used as comparative bearings.
Basic rating life of the mating track, track made from 42CrMo4 V, hardness 350 HV L = basic rating life in millions of overrolling motions Fr = radial load
|
![]() |
Wear of the mating track
Reduced wear of the mating track
The mating track wears to a lesser extent with the optimised INA profile ➤ Figure: mating track made from EN-GJS-500-7, mean value derived from several test runs after 360 000 overrolling motions.
Wear of the mating track, track made from EN-GJS-500-7 sw = wear Fr1 = low radial load Fr2 = high radial load
|
![]() |
Mating track made from 58CrV4, mean value derived from several test runs after 800 000 overrolling motions ➤ Figure.
Wear of the mating track, track made from 58CrV4 sw = wear Fr1 = low radial load Fr2 = high radial load
|
![]() |
Rigidity in outer ring contact
Radial deflection
The radial deflection of the outer ring and rolling element set is smaller for bearings with an optimised INA profile than for bearings with the profile R = 500 mm ➤ Figure. Example, yoke type track roller NUTR15.
Rigidity in outer ring contact δr = radial deflection Fr = radial load
|
![]() |
Corrosion protection by Corrotect
A Corrotect coating is often more economical than using corrosion-resistant steels
Track rollers are often subjected to aggressive media. In such applications, corrosion protection is therefore a decisive factor in achieving a long operating life of the bearings. In principle, corrosion-resistant steels may be used here. In many applications, however, the application of a special coating using available Corrotect thin film coating technology is more cost‑effective and should therefore be queried in advance. The series PWTR..‑2RS-RR and PWKR(E)..-2RS-RR are therefore available with a Corrotect coating. These bearings have the suffix RR ➤ section. Other series are also available as a special design with high performance Corrotect systems, which are matched to the specific application.
Before Corrotect-coated units are used, compatibility with the existing media should always be checked.
Corrotect systems
Corrotect coating thicknesses
Corrotect methods are available which permit the application of an extremely thin coating and, as a result, do not need to be included in the bearing tolerance (0,5 μm to 3 μm or 2 μm to 5 μm). Increased demands on corrosion protection can be fulfilled with increasing coating thicknesses or completely different Corrotect methods. In isolated cases, dimensional changes resulting from the coating must be taken into account in a further processing step.
Cr(VI)-free coatings
The current Corrotect systems are all free from Cr(VI), protect effectively against corrosion and, as a result, extend the useful life of the Schaeffler components ➤ Figure.
Further detailed information on the modular coating tool box and on the individual coating systems can be found in Technical Product Information TPI 186 “Higher Performance Capacity through the Use of Coatings”. This publication can be requested from Schaeffler.
Fitting of Corrotect-coated bearings
Take account of larger tolerances
The tolerances are increased by the thickness of the coating. In order to reduce the press-in forces, the surface of the parts should be lightly greased for fitting.
Uncoated and coated stud type track roller in the salt spray test |
![]() |
Load carrying capacity
Suitable for high radial loads
The bearings can support high radial loads as well as axial loads arising from slight misalignment and skewed running.
Installation as yoke or stud type track roller
If used as a yoke and stud type track roller, the outer rings undergo elastic deformation
If the yoke and stud type track rollers are used on a flat mating track, the outer rings undergo elastic deformation. Compared with rolling bearings supported in a housing bore, yoke and stud type track rollers therefore have the following characteristics:
- modified load distribution in the bearing. This is taken into consideration by the effective basic load ratings Cr w and C0r w used in the calculation of the rating life
- bending stresses and reverse bending strengths in the outer ring. These are taken into consideration by the permissible effective radial loads Fr per and F0r per. The bending stresses and reverse bending strengths must not exceed the permissible strength values of the material
Permissible radial load under dynamic loading
Cr w is valid
For rotating bearings under dynamic load, the effective basic dynamic load rating Cr w is used. Cr w is used to calculate the basic rating life.
The permissible dynamic radial load Fr per must not be exceeded. If a value for Fr per is not given, the effective basic dynamic load rating Cr w is used as a substitute. This basic load rating must not be exceeded by the radial load present. If the basic static load rating C0r w is lower than the basic dynamic load rating Cr w, then C0r w applies.
Permissible radial load under static loading
C0r w is valid
For bearings under static load, either stationary or with only infrequent rotary motion, the effective basic static load rating C0r w applies. C0r w is used to calculate the static load safety factor S0.
The permissible basic static radial load F0r per must not be exceeded. If a value for F0r per is not given, the effective basic static load rating C0r w is used as a substitute. This basic load rating must not be exceeded by the radial load present. In addition to the permissible radial load of the bearing, the permissible radial load of the mating track must also be taken into consideration ➤ link.
Angular misalignment
Skewed running
Additional axial load under skewed running
Skewed running leads to additional axial load on the rolling bearing and axial slippage in the rolling contact between the outer ring and mating track ➤ Figure. Depending on the skewed running angle α and the lubrication, wear can occur in these cases.
A complete loss of adhesive friction between the outer ring and raceway, with correspondingly severe wear, is to be expected with a skewed running angle α ≧ 1,4 · 10-4 · pH (°) or α ≧ 2,5 · 10-3 · pH (mrad).
Skewed running α = skewed running angle |
![]() |
Tilting
Cylindrical outer ring
If tilting occurs during running, increased edge stresses occur, especially in yoke and stud type track rollers with cylindrical outer rings.
Crowned outer ring
Track rollers with a crowned outer ring are less sensitive to tilting and should therefore be used in preference.
Limits for tilting
In practice, track rollers with a cylindrical outside surface and a tilting angle of β > 0,1° (1,7 mrad) and for yoke and stud type track rollers wth a crowned outside surface and a tilting angle of β > 0,25° (4,4 mrad) have proved susceptible to damage ➤ Figure.
Tilting β = tilt angle |
![]() |
Lubrication
Two contact zones
Lubricate the rolling elements, rolling element raceway and mating track
Two contact zones must be lubricated and considered separately:
- the rolling elements and rolling element raceway
- the outside surface of the track roller and the mating track
The contact zone between the rolling elements and the rolling element raceway is covered in the section Technical Principles, Lubrication.
Lubrication of the bearing
Greased with a lubricating grease to GA08
For yoke and stud type track rollers, a lithium complex soap grease with a mineral oil base and EP additives to GA08 is used. Yoke type track rollers can be lubricated via the inner ring, stud type track rollers have a type-dependent relubrication facility via the roller stud. Greases for initial greasing are listed in the chapter Lubrication ➤ Table. For relubrication, greases in accordance with ➤ Table are suitable.
In stud type track rollers with an eccentric collar, the eccentric collar covers the radial lubrication hole in the shank. Relubrication must therefore be carried out via the end faces.
Arcanol rolling bearing greases for relubrication
Arcanol grease |
Designation |
Type of grease |
Track roller |
---|---|---|---|
Load150 |
KP2N–20 |
Lithium soap grease with mineral oil base |
Yoke and stud type roller bearing track rollers |
Load220 |
KP2N–20 |
Lithium calcium soap grease with mineral oil base |
Yoke and stud type roller bearing track rollers |
Multi2 |
KP3K–30 |
Lithium soap grease with mineral oil base |
Yoke and stud type ball bearing track rollers |
Lubrication of mating track
Suitable lubricants
For lubrication of the mating track, all lubricants suitable for rolling bearing lubrication may be used. However, there are applications in which the mating track must not be lubricated.
If the contact point cannot be lubricated, wear must be expected, especially under high loads and at high speeds.
Oil lubrication
For oil lubrication, oils of type CLP to DIN 51517 are recommended.
Grease lubrication
For grease lubrication, lithium soap greases to DIN 51825 should be used. Relubrication intervals can only be determined under operating conditions. Relubrication must be carried out at the latest when fretting corrosion first occurs; this can be identified by a reddish discolouration of the mating track or the outer ring.
Solid lubricants and anti‑friction coatings
These substances are also suitable for lubrication. At high traverse or rotational speeds, however, they provide effective lubrication for a significantly shorter period than oil or grease lubrication.
Central lubrication system for stud type track rollers
Connection adapter with rapid-fit connection cartridge
If a central lubrication system is to be used, a patented central lubrication adapter can be used to connect the standard roller stud of stud type track rollers with hexagonal sockets on both sides ➤ Figure. This connector comprises a connection adapter with a hexagonal end and a rapid-fit connection cartridge.
The connection adapter is connected to the roller stud on one end of the stud type track roller by replacing the funnel type lubrication nipple with the fitting cylinder. The hexagonal end prevents rotation of the adapter. The other end of the stud type track roller is closed off using the supplied funnel type lubrication nipple ➤ Figure.
Central lubrication adapter and funnel type lubrication nipple
|
![]() |
Hard PA pipes should be used in preference
The connection adapter has an M10×1 internal thread. This is used for screw mounting and sealing of the rapid-fit connection cartridge. The cartridge gives firm retention and sealing of the plastic tube. It is therefore not necessary to screw the pipe and adapter onto each other. Hard PA pipes should be used in preference. In this instance, the operating limits according to DIN 73378 and the manufacturer's guidance must be observed. The maximum excess pressure for pipes made from PA11 or PA12 is as follows at +23 °C: 31 bar to 62 bar. The maximum excess pressure when using other screw-in connectors is 80 bar.
Dimensions
For dimensions of the adapters ➤ Table and ➤ Figure.
Dimensions of adapter
Central |
Dimensions |
|||||
---|---|---|---|---|---|---|
W |
L |
l1 |
l2 |
l3 |
For polyamide pipe to DIN 73378 |
|
Designation |
max. |
approx. |
d1×snom |
|||
AP8 | 8 | 27 | 16 | 22 | 4 |
4×0,75 |
AP10 | 10 | 27 | 15 | 22 | 5 |
4×0,75 |
AP14 | 14 | 25 | 8 | 20 | 6 |
4×0,75 |
Dimensions of central lubrication adapters |
![]() |
Calculation of relubrication intervals
Simplified determination of lubrication impulses
The relubrication quantities for central lubrication using flowable grease and their conversion to the number of relubrication impulses for conventional metering nipple sizes are given in the table ➤ Table. The data are valid for EP additives, for a lithium soap flowable grease with a mineral oil base ISO VG 100 to ISO VG 220 or NLGI 00 or NLGI 000.
Relubrication quantities for stud type track rollers
Series1) |
Outside diameter |
Central lubrication adapter |
Relubrication quantity2) |
Relubrication impulses |
||
---|---|---|---|---|---|---|
D |
Designation |
30 mm3 |
50 mm3 |
|||
mm |
g |
|||||
from |
up to |
|||||
NUKR, NUKRE | ||||||
35 |
40 |
AP8 |
1,1 |
40 |
24 |
|
47 |
52 |
AP10 |
2,4 |
89 |
53 |
|
62 |
90 |
AP14 |
7,3 |
271 |
163 |
|
KR, KRE | ||||||
35 |
40 |
AP8 |
1,2 |
44 |
27 |
|
47 |
52 |
AP10 |
1,6 |
60 |
36 |
|
62 |
90 |
AP14 |
6 |
222 |
133 |
|
KRV, KRVE | ||||||
35 |
40 |
AP8 |
0,7 |
26 |
16 |
|
47 |
52 |
AP10 |
1 |
37 |
22 |
|
62 |
90 |
AP14 |
3,2 |
120 |
72 |
- For stud type track rollers with hexagonal socket on both sides.
- Relubrication quantity and relubrication intervals for central lubrication using flowable grease for the majority of applications. Note the quantity required to fill the feed lines.
Relubrication periods
Approximate definition
The approximate definition of the relubrication periods for single shift operation and the majority of load applications is shown in ➤ Table and ➤ Table. The data are valid for single shift operation; the relubrication quantity and relubrication intervals are valid for the majority of applications. They are based on approximate calculation of the relubrication interval tfR. For definition of the relubrication interval see chapter Relubrication ➤ section. Within these periods, the number of relubrication intervals determined in accordance with ➤ Table should be evenly distributed.
Relubrication period for calculating the relubrication intervals
Load ratio C0r w/Pr |
Maximum operating speed nmax in % of nD G |
|||
---|---|---|---|---|
10 |
25 |
50 |
100 |
|
5 >C0r w/Pr ≧ 3 |
1/2 yearly |
‒ |
‒ |
‒ |
10 >C0r w/Pr ≧ 5 |
yearly |
4 months |
monthly |
‒ |
C0r w/Pr ≧ 10 |
yearly |
8 months |
2 months |
14 days |
Periods in single shift operation
Months |
Weeks |
Working days |
Working hours |
---|---|---|---|
1/2 |
2 |
10 |
80 |
1 |
4 |
20 |
160 |
2 |
8 |
40 |
320 |
4 |
16 |
80 |
640 |
6 |
24 |
120 |
960 |
8 |
32 |
160 |
1 280 |
12 |
48 |
240 |
1 920 |
Fitting of central lubrication adapter
Mount the stud type track roller first
The stud type track roller must be mounted before fitting the adapter. The unused relubrication hole in the roller stud must be closed off using the funnel type lubrication nipple supplied. Only the lubrication nipples supplied should be used.
Guidelines for mounting of the adapter
The central lubrication adapter should preferably be pressed in using a manual lever press under low, uniform pressure or carefully driven into the unused hexagonal socket of the roller stud by means of light blows with a plastic hammer; pay attention to the press-in depth l3 and the position of the hexagon ➤ Figure and ➤ Table.
Fitting of the polyamide pipe
The plastic pipe must be cut off straight across and inserted into the cartridge until it stops. Only polyamide pipes to DIN 73378 should be used. Check the seating of the pipe. Note maximum pressures, maximum temperatures and minimum bending radius. The maximum pipe length up to the distributor is 1 m.
Sealing
Yoke type track rollers
Available in open or sealed designs
Yoke type track rollers are available in open designs and with non-contact or contact type seals ➤ Table.
Seals used in yoke type track rollers
Yoke type track roller |
Seal |
---|---|
STO |
Open |
RSTO |
Open |
RNA22..-2RSR |
Lip seal on both sides |
NA22..-2RSR |
Lip seal on both sides |
PWTR..-2RS |
Protected lip seal on both sides |
continued ▼ |
Seals used in yoke type track rollers
Yoke type track roller |
Seal |
---|---|
NATR..-PP |
Three-stage sealing by plastic axial plain washers |
NATV..-PP |
Three-stage sealing by plastic axial plain washers |
NATR |
Gap seal on both sides |
NATV |
Gap seal on both sides |
NUTR |
Labyrinth seal on both sides |
NNTR..-2ZL |
Contact washer with lamellar ring on both sides |
continued ▲ |
Stud type track rollers
Available with seals on both sides
Stud type track rollers are sealed on both sides. Depending on the series, non-contact or contact types seals are used. A three-stage seal, comprising plastic axial plain washers with formed seal lips on both sides of the bearings, is also used ➤ Table.
Seals used in stud type track rollers
Stud type track roller |
Seal |
---|---|
KR |
Gap seal on both sides |
KR..-PP |
Three-stage sealing by plastic axial plain washers |
KRE..-PP |
Three-stage sealing by plastic axial plain washers |
KRV..-PP |
Three-stage sealing by plastic axial plain washers |
NUKR |
Labyrinth seal on both sides |
NUKRE |
Labyrinth seal on both sides |
PWKR..-2RS |
Protected lip seal on both sides |
PWKRE..-2RS |
Protected lip seal on both sides |
Three-stage seal
Seal design
In the three-stage concept, there is a gap seal between the plastic axial plain washer and the outer ring, as well as a labyrinth seal between the formed seal lip and an undercut in the outer ring. The disc spring shape of the axial plain washer gives a preloaded contact seal as the third stage. It also provides axial sliding contact between the outer ring and contact washers, thus reducing wear and grease consumption.
Speeds
Speeds nD G
The maximum possible speed is essentially determined by the permissible operating temperature of the yoke and stud type track rollers. The temperature thus depends on the type of bearing, the load, the lubrication conditions and the cooling conditions.
Speeds with lip seals
The speed of track rollers with lip seals is additionally restricted by the permissible sliding speed at the seal lip.
Speed during continuous operation
Criteria for guide values
The speeds nD G in the product tables are guide values. They were determined for:
- grease lubrication
- loads during continuous operation of < 0,05 · C0r w
- skewed running angles of α < 0,03° (< 0,5 mrad)
- an ambient temperature of +20 °C
- outer ring temperatures of +70 °C
- lubricated mating tracks
- no external axial load
Reducing the speed
The speeds must be reduced under the following conditions:
- loads > 0,05 · C0r w
- additional axial forces (skewed running)
- insufficient heat dissipation
Higher speeds
Higher speeds can be achieved with intermittent operation and oil impulse lubrication.
Noise
Schaeffler Noise Index
The Schaeffler Noise Index (SGI) is not yet available for this bearing type ➤ link. The data for these bearing series will be introduced and updated in stages.
Temperature range
Limiting values
The operating temperature of the yoke and stud type track rollers is limited by:
- the dimensional stability of the bearing rings and rolling elements
- the cage
- the lubricant
- the seals
Permissible temperature ranges
Operating temperature |
Yoke and stud type track rollers |
|||||||
---|---|---|---|---|---|---|---|---|
Open or with |
With |
With |
With |
|||||
2RS, 2RSR |
TV |
PP |
||||||
from |
to |
from |
to |
from |
to |
from |
to |
|
°C |
||||||||
|
–30 |
+140 |
–30 |
+120 |
–30 |
+120 |
–30 |
+100 |
Note the information on the operating temperature range in Technical Principles, Lubrication.
In the event of anticipated temperatures which lie outside the stated values, please contact Schaeffler.
Cages
Yoke type track rollers
Yoke type track rollers without inner ring
With cage
Yoke type track rollers RSTO and RNA22..-2RSR have a sheet steel cage as standard. Yoke type track rollers RSTO up to D = 24 mm have a plastic cage made from polyamide PA66 (suffix TV). Series RSTO does not have axial guidance of the needle roller and cage assembly and of the outer ring. As a result, lateral guidance is required.
Yoke type track rollers with inner ring
With cage, with full complement needle roller or cylindrical roller set
The series STO, NA22..-2RSR, NATR and NATR..-PP have a sheet steel cage as standard. Yoke type track rollers STO up to D = 24 mm have a plastic cage made from polyamide PA66 (suffix TV). The series NATV and NATV..-PP have a full complement needle roller set, while yoke type track rollers NUTR, PWTR..-2RS and NNTR..-2ZL have a full complement cylindrical roller set. Series STO does not have axial guidance of the needle roller and cage assembly and of the outer ring. As a result, lateral guidance is required.
Stud type track rollers
Stud type track rollers without eccentric collar
With cage, with full complement needle roller or cylindrical roller set
Stud type track rollers KR and KR..-PP have a sheet steel cage, the design KRV..-PP has a full complement needle roller set. The series NUKR and PWKR..-2RS have a full complement cylindrical roller set.
Axial guidance of outer ring
In KR, axial guidance is provided directly by the contact flange and contact washer, while in KR..-PP and KRV..-PP this is provided by plastic axial plain washers, the contact flange and contact washer. In NUKR, the outer ring is guided axially by the rolling elements, in PWKR, axial guidance of the outer ring is provided by the central rib and rolling elements.
Stud type track rollers with eccentric collar
With cage or full complement cylindrical roller set
Series KRE..-PP has a sheet steel cage, NUKRE and PWKRE..-2RS have a full complement cylindrical roller set.
Axial guidance of outer ring
In KRE..-PP, axial guidance is provided by the plastic axial plain washers, contact flange and contact washer. In NUKRE, the outer ring is guided axially by the rolling elements, in PWKRE, axial guidance of the outer ring is provided by the central rib and rolling elements.
Internal clearance
Radial internal clearance
Standard corresponds approximately to C2 or CN
The radial internal bearing clearance of yoke and stud type track rollers corresponds approximately to tolerance class C2 (Group 2) and, in the case of STO and NA22..-2RSR, to tolerance class CN (Group N). Values ➤ Table.
The values for radial internal clearance correspond to DIN 620-4:2004 (ISO 5753-1:2009). These are valid for bearings which are free from load and measurement forces (without elastic deformation).
Radial internal clearance for yoke and stud type track rollers
Nominal |
Radial internal clearance |
||||||||
---|---|---|---|---|---|---|---|---|---|
d |
C2 |
CN |
C3 |
C4 |
|||||
mm |
μm |
μm |
μm |
μm |
|||||
over |
incl. |
min. |
max. |
min. |
max. |
min. |
max. |
min. |
max. |
‒ |
24 |
0 |
25 |
20 |
45 |
35 |
60 |
50 |
75 |
24 |
30 |
0 |
25 |
20 |
45 |
35 |
60 |
50 |
75 |
30 |
40 |
5 |
30 |
25 |
50 |
45 |
70 |
60 |
85 |
40 |
50 |
5 |
35 |
30 |
60 |
50 |
80 |
70 |
100 |
50 |
65 |
10 |
40 |
40 |
70 |
60 |
90 |
80 |
110 |
65 |
80 |
10 |
45 |
40 |
75 |
65 |
100 |
90 |
125 |
80 |
100 |
15 |
50 |
50 |
85 |
75 |
110 |
105 |
140 |
100 |
120 |
15 |
55 |
50 |
90 |
85 |
125 |
125 |
165 |
120 |
140 |
15 |
60 |
60 |
105 |
100 |
145 |
145 |
190 |
Dimensions, tolerances
Tolerances
The dimensional and running tolerances correspond to the tolerance class Normal in accordance with ISO 492, for KR, KRE and KRV to ISO 7063.
Deviations from ISO 492
The following deviations from ISO 492 apply:
- the diameter deviations of the profiled outside surface 0/–0,05 mm
- for NNTR, the diameter tolerance class h10
- for NATR, NATV, NUTR, PWTR..-2RS, the tolerance class h12 for width B
- for NATR, NATV, the roundness of the inner ring
- for stud type track rollers, the tolerance class of the shank diameter h7 and the eccentric collar diameter h9
Tolerances for Corrotect-coated bearings
For PWTR..-2RS-RR and PWKR..-2RS-RR , the tolerances are increased by the thickness of the Corrotect special coating.
Enveloping circle
Yoke type track rollers without inner ring
For yoke type track rollers without an inner ring, RSTO and RNA22..-2RSR, the needle enveloping circle Fw is in the tolerance class F6. The enveloping circle is the inner inscribed circle of the needle rollers in clearance-free contact with the adjacent construction.
Suffixes
For a description of the suffixes used in this chapter ➤ Table and medias interchange http://www.schaeffler.de/std/1B69.
Suffixes and corresponding descriptions
Suffix |
Description of suffix |
|
---|---|---|
PP |
Plastic axial plain washer with formed seal lip on both sides of the bearing, giving a three-stage seal |
Standard |
RR |
Protected against corrosion by Corrotect special coating in the case of PWTR..-2RS and PWKR(E)..-2RS |
Standard |
SK |
Hexagonal socket only on the flange-side end face, no relubrication facility |
Standard |
TV |
Plastic cage |
Standard |
XL |
X-life design |
Standard |
2RS |
Protected lip seal on both sides |
Standard |
2RSR |
Radial contact lip seal on both sides |
Standard |
2ZL |
Contact washer with lamellar ring on both sides |
Standard |
Structure of bearing designation
Examples of composition of bearing designation
The designation of bearings follows a set model. Examples ➤ Figure to ➤ Figure.
Yoke type track roller, single row, without inner ring, without seal, without axial guidance, open design, plastic cage, R = 500: designation structure |
![]() |
Yoke type track roller, double row, with inner ring, sealed, optimised INA profile: designation structure |
![]() |
Needle roller stud type track roller, full complement needle roller set, with axial guidance, three-stage seal, optimised INA profile: designation structure |
![]() |
Cylindrical roller stud type track roller, full complement needle roller set, with axial guidance, X-life design, optimised INA profile: designation structure |
![]() |
Dimensioning
Calculation of the rating life
The methods for calculating the rating life are:
- the basic rating life to DIN ISO 281
- the adjusted basic rating life to DIN ISO 281
- the expanded calculation of the adjusted reference rating life to DIN ISO 281-4
Use effective basic dynamic/static load ratings
These methods are described in the chapter Load carrying capacity and life. For yoke and stud type track rollers, use the following values (values ➤ link):
- for Cr, the effective basic dynamic load rating Cr w
- for C0r, the effective basic static load rating C0r w
- for Cur, the effective fatigue limit load Cur w
Other rating life equations
Other equations for calculating the rating life ➤ Equation, ➤ Equation and ➤ Equation.
Basic rating life
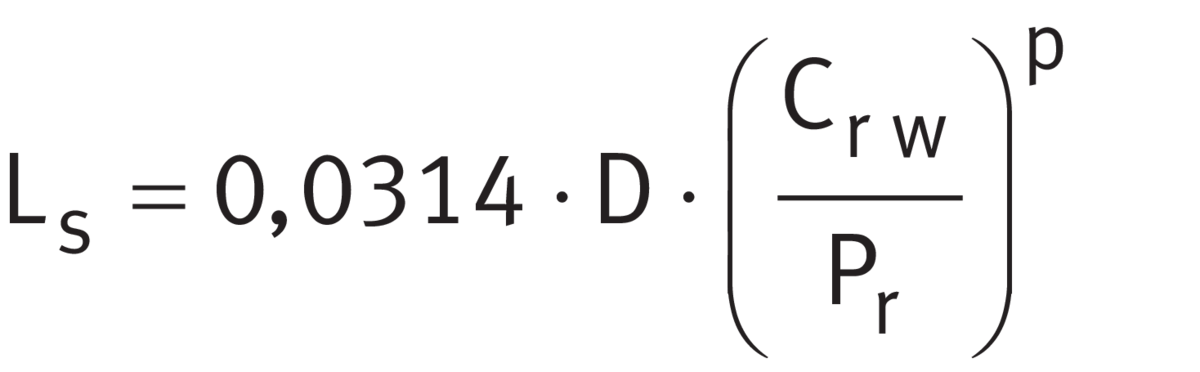
Basic rating life in oscillating operation
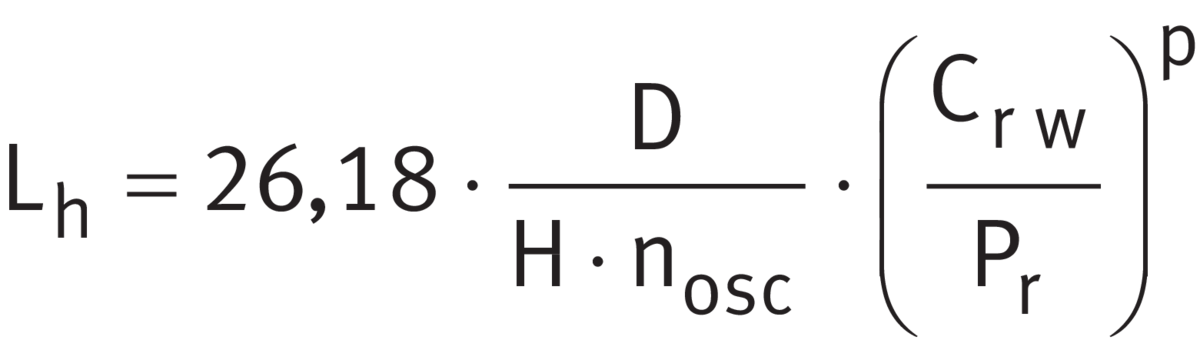
Basic rating life
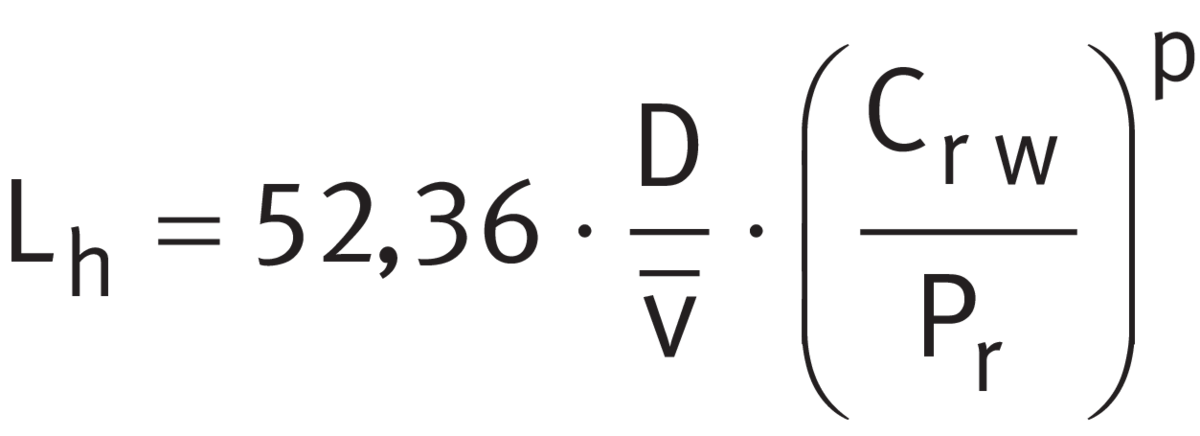
Legend
Ls | 105 m |
Basic rating life in 105 m |
Lh | h |
Basic rating life in operating hours |
Cr w | N |
Effective basic dynamic load rating. Cr w is that load of constant magnitude and direction which a sufficiently large group of apparently identical track rollers can endure for a basic rating life of one million revolutions |
Pr | N |
Equivalent dynamic bearing load (radial load) |
p | - |
Life exponent: |
n | min–1 |
Operating speed |
D | mm |
Outside diameter of track roller |
H | m |
Single stroke length for oscillating motion |
nosc | min–1 |
Number of return strokes per minute |
![]() |
m/min |
Mean travel velocity |
Operating life
Life actually achieved
The operating life is defined as the life actually achieved by a yoke type track roller, stud type track roller or ball bearing track roller. This can deviate significantly from the calculated basic rating life.
Cause of deviations
Possible causes of a deviation between the basic rating life and the operating life are wear or fatigue as a result of:
- deviations in the operating data
- misalignment between the track roller and mating track
- insufficient or excessive operating clearance
- contamination of the track roller
- inadequate lubrication
- excessive operating temperature
- oscillating bearing motion with very small swivel angles, leading to false brinelling
- wear between the outer ring outside surface and mating track
- high vibration and false brinelling
- very high shock loads, static overloading
- prior damage during mounting
Due to the variety of mounting and operating conditions, the operating life cannot be precisely calculated in advance. The most reliable way of arriving at a close estimate is by comparison with similar applications.
Static load safety factor
S0 = C0r w/F0r
In addition to the basic rating life L, it is also always necessary to check the static load safety factor S0 ➤ Equation.
Static load safety factor
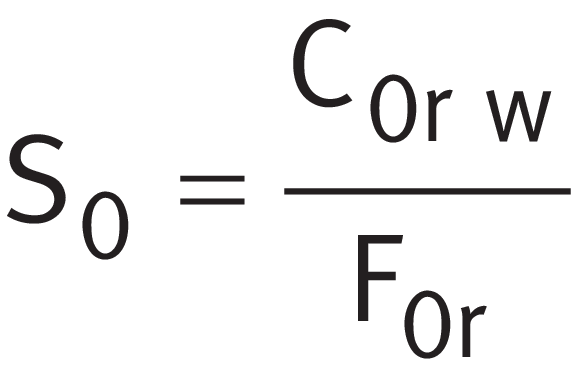
Legend
S0 | - |
Static load safety factor |
C0r w | N |
Effective radial basic static load rating in accordance with product table |
F0r | N |
Maximum static radial load on track roller |
Track rollers are regarded as heavily loaded at a static load safety factor of S0 < 8. Static load safety factors of S0 < 1 cause plastic deformation of the rolling elements and the raceways, which can impair smooth running. This is only permissible for bearings with small rotary motions or in secondary applications.
If an application has a static load safety factor of S0 < 2, please consult Schaeffler.
Frictional torque
Calculation only possible in approximate terms
The frictional torque MR of a yoke type, stud type or ball bearing track roller depends on many influencing factors such as load, speed and type, as well as the lubrication conditions and seal friction. Due to the wide range of these influencing factors, the frictional torque can only be calculated approximately.
For designs without contact seals, the frictional torque can be calculated under normal operating conditions and moderate speed range in accordance with ➤ Equation.
Frictional torque
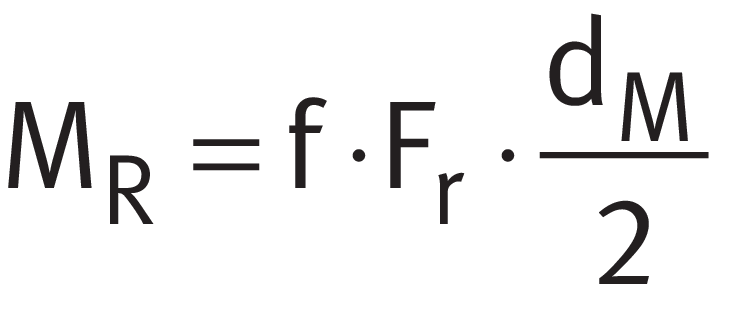
Legend
MR | Nmm |
Frictional torque of track roller |
f | - | |
Fr | N |
Radial load |
dM | mm |
Mean bearing diameter of track roller (d + D)/2 |
Coefficient of friction for yoke and stud type track rollers
Type |
Coefficient of friction |
|
---|---|---|
f |
||
Cylindrical roller bearing, full complement |
0,002 |
to 0,003 |
Needle roller bearing, with cage |
0,003 |
to 0,004 |
Needle roller bearing, full complement |
0,005 |
to 0,007 |
Coefficient of friction for track rollers
Type |
Coefficient of friction |
|
---|---|---|
f |
||
Ball bearing, single row |
0,0015 |
to 0,002 |
Ball bearing, double row |
0,002 |
to 0,003 |
Validity of coefficients of friction
The stated factors f are valid for yoke type, stud type and ball bearing track rollers, which are unsealed or have a contact seal and are subjected to radial load. If sealed designs are used, higher coefficients of friction must be expected.
Influence of additional axial forces
Additional axial forces, such as those occurring under large skewed running angles, can lead to a substantial increase in the values, especially in the case of track rollers based on needle rollers. Track rollers based on ball bearings can support axial loads without a significant change in friction.
Displacement resistance
When an outer ring rolls on a track, it must overcome not only the friction within the bearing but also the rolling friction between the outer ring and the mating track. The displacement resistance is determined from the rolling friction and the frictional torque MR in accordance with ➤ Equation.
Displacement resistance
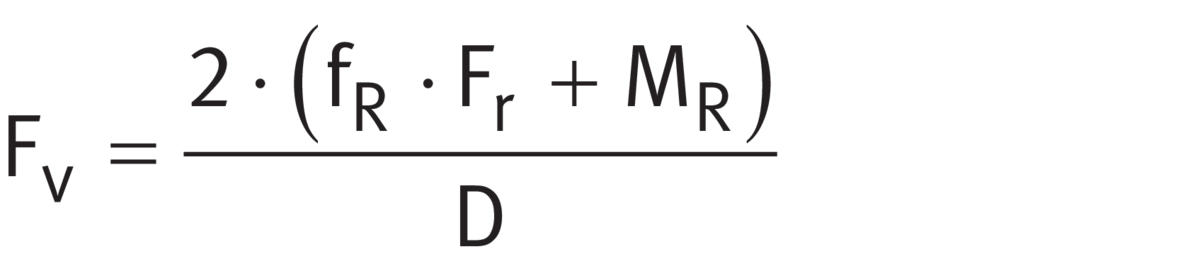
Legend
Fv | N |
Displacement resistance |
fR | mm |
Coefficient of rolling friction for tracks made from hardened steel: |
Fr | N |
Radial load |
MR | Nmm |
Frictional torque |
D | mm |
Outside diameter of track roller |
Minimum load
Minimum load C0r w/Fr < 60
In order to ensure that the outer ring is driven, that no slippage occurs and that the track roller does not lift from the mating track, the track roller must be subjected to a minimum load in dynamic operation. In general, the minimum load is calculated using the ratio C0r w/Fr < 60.
Design of bearing arrangements
Adjacent construction for yoke type track rollers
Yoke type track rollers without inner ring, raceway design
For yoke type track rollers without an inner ring, the rolling element raceway on the shaft or stud must be hardened and ground ➤ Table. The surface hardness must be 670 HV to 840 HV, the hardening depths CHD or SHD must be sufficiently large.
Tolerances and surface design
Diameter tolerance of shafts or studs |
Roughness |
Roundness tolerance |
Parallelism tolerance |
|
---|---|---|---|---|
Without inner ring |
With inner ring |
max. |
max. |
|
k5 Ⓔ |
g6 Ⓔ |
Ramax 0,4 (Rzmax 2) |
25% of diameter tolerance |
50% of diameter tolerance |
Location of yoke type track rollers without axial guidance
For yoke type track rollers without axial guidance, the outer ring and needle roller and cage assembly must be laterally guided ➤ Figure. The axial contact surfaces for the outer rings must be precision machined (Ramax 2 recommended), wear-resistant and lubricated.
Bearing parts must not be interchanged with parts from other bearings during fitting
Yoke type track rollers without axial guidance are not self-retaining. The outer ring and the needle roller and cage assembly are matched to each other and must not be interchanged during mounting with components from other bearings of the same size. The inner rings are matched to the enveloping circle class F6 and can be interchanged within their accuracy class (used in different combinations).
Lateral guidance of outer ring and needle roller and cage assembly
|
![]() |
Location of yoke type track rollers with axial guidance
Observe dimension d2
Yoke type track rollers with axial guidance must be axially clamped in place. The thrust washers must be axially supported if axial loads occur. The dimension d2 in the product tables must be observed ➤ Figure.
Location by snap ring
Yoke type track rollers NATR and NATV can be located using conventional fasteners such as snap rings ➤ Figure.
Location by snap ring d2 = abutment diameter
|
![]() |
Firmly locate inner ring and thrust ring axially
For yoke type track rollers NNTR..-2ZL, NUTR and PWTR..-2RS, the inner ring and thrust ring must be located axially ➤ Figure.
Clamping of inner ring and thrust washer
|
![]() |
Adjacent construction for stud type track rollers
Bore tolerance H7
The bore tolerance H7 produces a clearance fit since the stud tolerance is h7 for studs without eccentric collar and h9 for studs with eccentric collar.
Design of locating surfaces
The locating surfaces for stud type track rollers must be flat, perpendicular and of sufficient height. The strength of the nut locating surface must be sufficiently high. The dimension must not be less than the dimension d2 in the product tables.
Lead chamfer
The lead chamfer on the locating bore must not be more than 0,5×45°.
Axial location
Stud type track rollers must be axially secured using a hexagon nut. The nuts of grade 8 to ISO 4032 (M6, M8), ISO 8673, are not included in the delivery and must be ordered separately.
If heavy vibration occurs, the stud type track rollers can be located using self-locking nuts in accordance with DIN 985 or special locking washers.
For self-locking nuts, a higher tightening torque must be observed; the advice given by the nut manufacturer must be followed.
Position of lubrication hole
Ensure that the lubrication hole is positioned correctly
The position of the radial lubrication hole is indicated on the flanged side of the roller stud ➤ Figure. This must not be positioned in the loaded zone.
Position of lubrication hole
|
![]() |
Design of mating track
Take account of Hertzian pressure
In the design of the mating track (material and strength, heat treatment, surface), the Hertzian pressure pH must be taken into consideration. This is dependent on the load, the contact geometry (point contact or line contact) and the modulus of elasticity of the materials.
Nomogram for determining the Hertzian pressure
The Hertzian pressure can be read from the nomogram and calculated ➤ Figure. The nomogram is valid for mating tracks made from steel. For other materials, the correction factor k must be taken into consideration ➤ Table.
Additional conditions
Other conditions:
- point contact
- radius of curvature R = 500. For radii R > 500 and the optimised INA profile, correction values must be calculated ➤ Equation
- mating track flat in the direction of the track roller axis
- signs according to ➤ Figure
Raceway radii and signs D = outside diameter of track roller rL = raceway radius |
![]() |
Example
NUKR35
- stud type track roller NUKR35 with optimised INA profile
- D = 35 mm
- outer ring width C = 18 mm
- radial load Fr = 2 500 N
- cam plate, radius rL = 80 mm
Curvature sum
Calculating the curvature sum
The curvature sum is calculated from the raceway radius rL and the diameter D of the track roller ➤ Equation.
Curvature sum
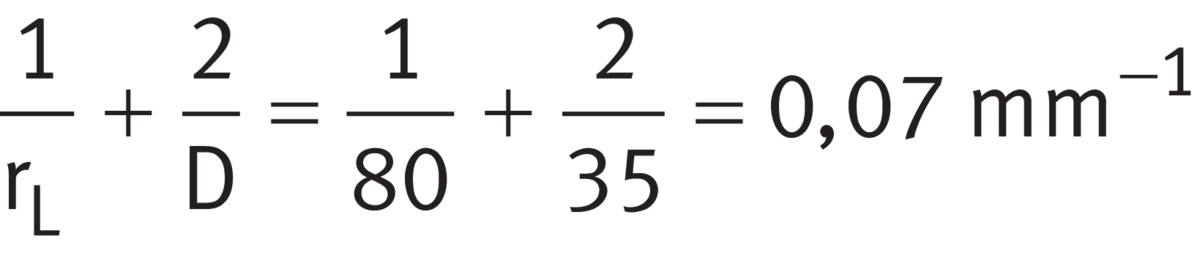
PH500 = 1 250 N/mm2
Hertzian pressure

= 1 250 N/mm2 · 0,85
= 1 063 N/mm2
(1 025 N/mm2 from calculation program BEARINX, kpH ➤ Table)
Nomogram for determining Hertzian pressure, calculation example (purple) |
![]() |
Track rollers with optimised INA profile
For an outer ring with the optimised INA profile, the following calculation provides sufficiently precise values ➤ Equation and ➤ Table.
Optimised INA profile

Pressure factor kpH
Outer ring width |
Pressure factor |
---|---|
C |
kpH |
mm |
|
10 ≦ C ≦ 15 |
1 |
15 < C ≦ 20 |
0,85 |
20 < C ≦ 30 |
0,83 |
30 < C ≦ 35 |
0,8 |
Radius of curvature R > 500 mm
If the outer ring has a radius of curvature of R > 500 mm, ➤ Equation.
R > 500 mm
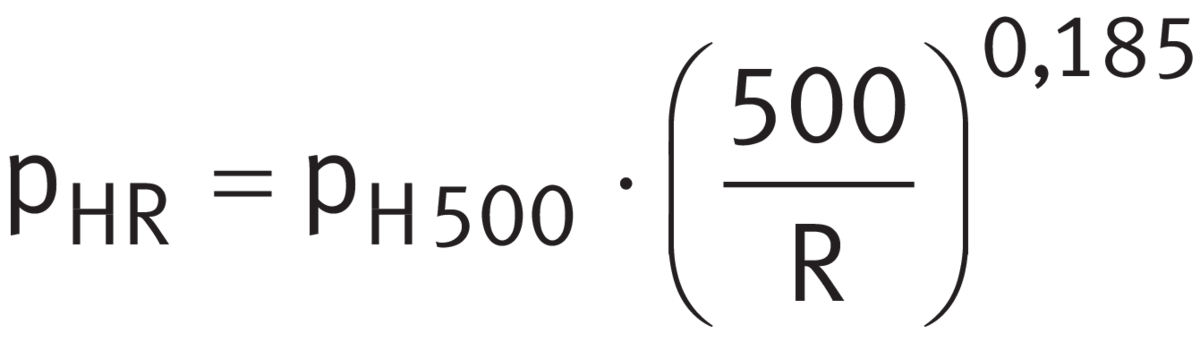
Materials for mating track
High load on the mating track
The mating track is subjected to high load during overrolling. This produces high Hertzian contact pressures. The strength and surface hardness of the material must be matched to this load.
Correction factors
For raceways subjected to high loads, through hardened steels, case hardened steels and steels for flame or induction hardening are recommended. For raceways subjected to low loads, construction steels and cast steel or cast iron materials can be used ➤ Equation ➤ Table.
Correction for mating track material

Correction factor k
Material |
Material no. |
Correction factor for mating track with |
|
---|---|---|---|
k |
|||
for point contact |
for line contact |
||
EN-GJL-200 |
0.6020 |
0,74 |
0,8 |
EN-GJL-300 |
0.6030 |
0,81 |
0,85 |
GG-40 |
‒ |
0,85 |
0,88 |
EN-GJS-400-15 |
0.7040 |
0,92 |
0,94 |
EN-GJS-600-3 |
0.7060 |
0,94 |
0,96 |
EN-GJS-800-2 |
0.7080 |
0,96 |
0,97 |
Guide values for permissible Hertzian pressure
Selection by material
The table ➤ Table gives a selection of materials with the associated values. The values were determined on steel test specimens; loadings of 10⁷ were achieved.
On a similar basis to the calculation of the load carrying capacity of rolling bearings, this gives:
- pH stat for predominantly static load
- pH dyn for predominantly dynamic load
Materials and guide values for permissible Hertzian pressure (selection)
Material |
Material designation |
Material no. |
Hertzian pressure |
Proof stress of material |
|||
---|---|---|---|---|---|---|---|
new |
old: |
pH stat |
pH dyn |
Rp0,2 |
|||
N/mm2 |
N/mm2 |
N/mm2 |
|||||
Flake graphite cast iron | |||||||
EN-GJL-150 |
GG-15 |
EN-JL1020 |
0.6015 |
850 |
340 |
120 |
|
EN-GJL-200 |
GG-20 |
EN-JL1030 |
0.6020 |
1 050 |
420 |
150 |
|
EN-GJL-250 |
GG-25 |
EN-JL1040 |
0.6025 |
1 200 |
480 |
190 |
|
EN-GJL-300 |
GG-30 |
EN-JL1050 |
0.6030 |
1 350 |
540 |
220 |
|
EN-GJL-350 |
GG-35 |
EN-JL1060 |
0.6035 |
1 450 |
580 |
250 |
|
GG-40 | ‒ | 1 500 | 600 | 280 | |||
Spheroidal graphite cast iron | |||||||
EN-GJS-400-15 |
GGG-40 |
EN-JS1030 |
0.7040 |
1 000 |
490 |
250 |
|
EN-GJS-500-7 |
GGG-50 |
EN-JS1050 |
0.7050 |
1 150 |
560 |
320 |
|
EN-GJS-600-3 |
GGG-60 |
EN-JS1060 |
0.7060 |
1 400 |
680 |
380 |
|
EN-GJS-700-2 |
GGG-70 |
EN-JS1070 |
0.7070 |
1 550 |
750 |
440 |
|
EN-GJS-800-2 |
GGG-80 |
EN-JS1080 |
0.7080 |
1 650 |
800 |
500 |
|
Cast steel | |||||||
GE200 |
GS-38 |
1.0420 |
780 |
380 |
200 |
||
GE240 |
GS-45 |
1.0446 |
920 |
450 |
230 |
||
GS-52 |
1.0552 |
1 050 |
510 |
260 |
|||
GE300 | GS-60 | 1.0558 | 1 250 | 600 | 300 | ||
GS-62 | ‒ | 1 300 | 630 | 350 | |||
GS-70 | ‒ | 1 450 | 700 | 420 | |||
Construction steel | |||||||
S235JR |
St 37-2 |
1.0037 |
690 |
340 |
235 |
||
S275JR |
St 44-2 |
1.0044 |
860 |
420 |
275 |
||
S355J2G3+N |
St 52-3 |
1.0570 |
980 |
480 |
355 |
||
Quenched and tempered steel | |||||||
C45 V |
1.0503 |
1 400 |
670 |
500 |
|||
Cf53 V |
1.1213 |
1 450 |
710 |
520 |
|||
Cf56 V | ‒ | 1 550 | 760 | 550 | |||
C60 V |
1.0601 |
1 600 |
780 |
580 |
|||
46Cr2 V |
1.7006 |
1 750 |
850 |
650 |
|||
42CrMo4 V |
1.7225 |
2 000 |
980 |
900 |
|||
50CrV4 V |
1.8159 |
2 000 |
980 |
900 |
|||
Hardened steel and with tempering at low temperatures | |||||||
100Cr6 H |
1.3505 |
4 000 |
1 500 |
1900 |
|||
16MnCr51) |
1.7131 |
4 000 |
1 500 |
7703) |
|||
Cf532) |
1.1213 |
4 000 |
1 500 |
7303) |
|||
Cf562) |
‒ |
4 000 |
1 500 |
7603) |
- Case hardened.
- Induction surface layer hardening.
- Proof stress of the core.
Hardenable materials
Suitable steels
The following materials with a purity level corresponding to that of alloyed construction steels may be used:
- through hardening steels to ISO 683-17, such as 100Cr6. In special cases, surface hardening is possible
- case hardening steels to ISO 683-17 such as 17MnCr5, or in accordance with EN 10084, such as 16MnCr5. Both the hardenability and the core strength must be taken into consideration. For case hardening, a fine grained hardening structure and a case hardening depth CHD in accordance with ➤ Equation is necessary
- steels for flame or induction hardening to ISO 683-17, such as C56E2, or to DIN 17212, such as Cf53. For flame or induction hardening, only the parts of the machine component used as raceways must be hardened. The material should be quenched and tempered before hardening. The surface hardening depth SHD is determined in accordance with ➤ Equation
Heat treatment of the mating track
Specifications for heat treatment
The following apply for hardened mating tracks:
- a surface hardness of 670 HV to 840 HV
- CHD and SHD according to ➤ Equation and ➤ Equation – in accordance with DIN 50190, the depth of the hardened surface zone at which there is still a hardness of 550 HV
- hardness curves according to ➤ Figure and ➤ Figure
- a hardening depth of ≧ 0,3 mm
The equations are based on the hardness curves normally achieved with skilled heat treatment.
Case hardening
Case hardening depth
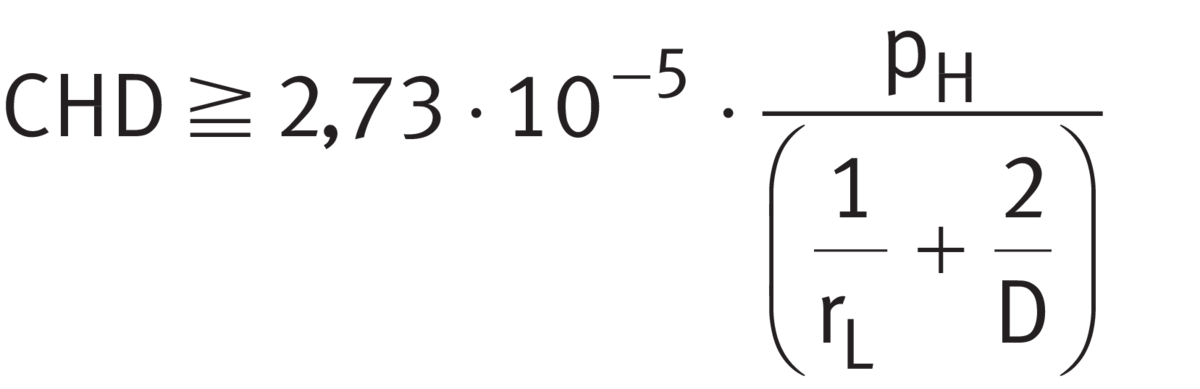
Flame and induction hardening
Surface hardening depth
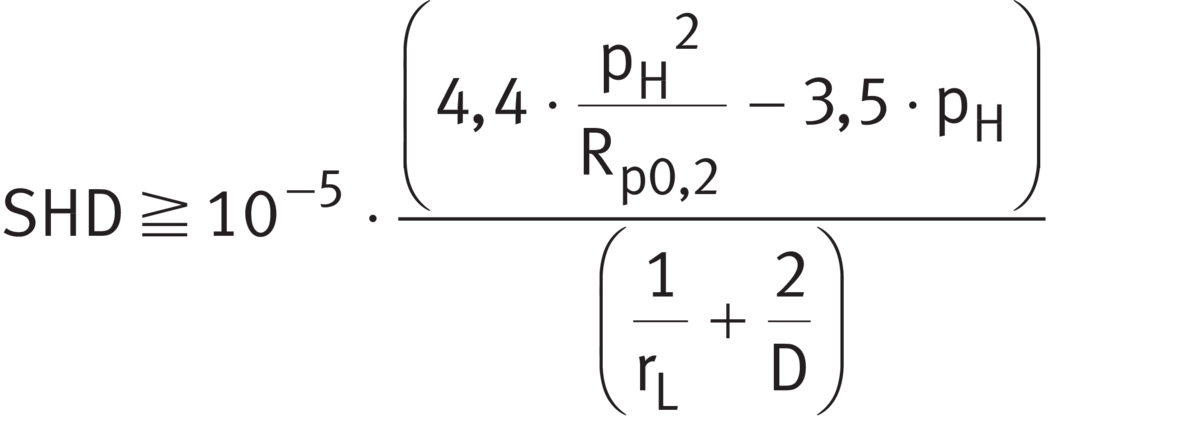
Legend
pH | N/mm2 |
Max. Hertzian pressure |
CHD | mm |
Case hardening depth |
SHD | mm |
Surface hardening depth |
D | mm |
Outside diameter of track roller |
Rp0,2 | N/mm2 |
Proof stress of mating track material ➤ Table |
rL | mm |
Radius of mating track – the raceway must be flat in the direction of the yoke type track roller axis ➤ Figure |
Case hardening depth CHD, hardness curve CHD = case hardening depth with hardness 550 HV HV = hardness z = distance from surface
|
![]() |
Surface hardening depth SHD, hardness curve SHD = surface hardening depth HV = hardness z = distance from surface
|
![]() |
Schaeffler guideways as mating tracks
Ready-to-fit units
The Schaeffler guideways are ready-to-fit units from the Schaeffler linear range. They are to the appropriate grade Q20 for yoke and stud type track rollers and correspond to the dimensions of standard profiles:
- parallelism 20 μm/m
- surface quality Ramax 0,8
- hardness 58 HRC to 62 HRC
- angular misalignment between the raceways max. 1 mrad (1 μm/mm)
- deviations of the guideway cross-section +0,05/+0,015
- length tolerance of the individual guideway +1/0 mm/m
Protection of mating track
The mating track must be protected against contamination. Where necessary, covers and wipers, for instance made from felt, should be placed ahead of the track roller ➤ Figure.
Protection of mating track against contamination
|
![]() |
Mounting and dismounting
Mounting
Track rollers must be handled with care before and during assembly. Their trouble-free operation depends largely on the care taken during mounting.
Guidelines for mounting
The products must be protected against dust, contaminants and moisture. Contaminants have a detrimental influence on the running and operating life of rolling bearings.
Do not cool the bearings excessively. Moisture due to condensation can lead to corrosion in the bearings and bearing seats.
Yoke type track rollers RSTO and STO are not self-retaining. The outer ring and the needle roller and cage assembly are matched to each other and must not be interchanged during mounting with components from other bearings of the same size.
The assembly area must be kept clean and free from dust.
Check the seat of the axis for dimensional and geometrical accuracy and cleanliness.
The seating surfaces of the bearing rings must be lightly oiled or rubbed with solid lubricant.
After mounting, the bearings must be supplied with lubricant. Finally, the correct functioning of the bearing arrangement must be checked.
Mounting tools
Depending on the application, the following are suitable:
- induction heaters; note the manufacturer’s guidance on grease and seals
- heating cupboard; heating up to +80 °C
- mechanical or hydraulic presses; use mounting sleeves that cover the whole circumference of the bearing ring end faces
- hammer and mounting sleeves; blows should only be applied concentrically to the sleeve
Mounting forces must never be directed through the rolling elements. Avoid direct blows on the bearing rings in all cases. Ensure that the seals are not damaged.
Guidelines for dismounting
Mounting should be taken into consideration in the original design of the bearing position. If the bearing is to be reused:
- avoid direct blows on the bearing rings
- dismounting forces should not be applied through the rolling elements
- carefully clean the bearings after dismounting
- do not use a concentrated or “hard” flame
Mounting and dismounting of yoke type track rollers (needle and cylindrical roller types)
Use a mounting press
If the tolerances are unfavourable, the yoke type track roller should be pressed onto the shaft or stud using a mounting press ➤ Figure. The inner ring must be mounted such that the pressing-in force is distributed uniformly over the end face of the inner ring.
Lubrication hole
The bearings must be mounted such that the lubrication hole is positioned in the unloaded zone. For yoke type track rollers PWTR and NNTR, defined positioning of the lubrication hole is not required.
Mounting of yoke type track roller using a mounting press NUTR
|
![]() |
Axial location
Yoke type track rollers NUTR, PWTR and NNTR must be axially clamped in place ➤ Figure.
Axial location PWTR..-2RS
|
![]() |
Mounting and dismounting of stud type track rollers (needle and cylindrical roller types)
Use a mounting press
Stud type track rollers should be mounted using a mounting press if possible ➤ Figure.
Blows on the flange of the roller stud must be avoided. The position of the lubrication hole is indicated on the flanged side of the roller stud. It must not be positioned in the loaded zone ➤ Figure.
Drive fit lubrication nipples for stud type track rollers
Fit the lubrication nipples before mounting the bearings
Stud type track rollers are supplied with loose drive fit lubrication nipples that must be pressed in correctly before mounting of the bearings ➤ Figure. For lubrication of stud type track rollers using the central lubrication adapter ➤ Figure.
Only the lubrication nipples supplied may be used ➤ Table. If relubrication is to be carried out via the locating bore, the axial lubrication holes in the stud type track roller must be closed off using the lubrication nipples before mounting ➤ Figure.
Stud type track roller with drive fit lubrication nipple and dimensions for pressing mandrel KR..-PP |
![]() |
Drive fit lubrication nipples
Lubrication nipple |
Dimensions |
Suitable for outside diameter D |
||||||
---|---|---|---|---|---|---|---|---|
D |
d |
L |
h |
dS |
LS |
|||
±0,1 |
||||||||
mm |
mm |
mm |
mm |
mm |
mm |
|||
NIPA1 |
6 |
4 |
6 |
1,51) |
‒ |
‒ |
16 and |
19 |
NIPA1×4,5 |
4,7 |
4 |
4,5 |
1 |
4,5 |
5 |
22 to |
32 |
NIPA2×7,5 |
7,5 |
6 |
7,5 |
2 |
7,5 |
6 |
35 to |
52 |
NIPA3×9,5 |
9,5 |
8 |
9,5 |
3 |
10 |
9 |
62 to |
90 |
- Projection of lubrication nipple, see product tables
Axial location of stud type track rollers
Secure bearings axially
Stud type track rollers must be axially secured using a hexagon nut. The slot or hexagonal socket on the end of the roller stud can be used to hold the bearing by means of a key while tightening the fixing nut and to adjust the eccentric collar ➤ Figure. If heavy vibration occurs, self-locking nuts to DIN 985 or special locking washers can be used.
The tightening torque for the fixing nuts stated in the product tables must be observed. It is only in this way that the permissible radial load can be ensured. If this cannot be adhered to, an interference fit is required. For self-locking nuts, a higher tightening torque must be observed; the advice given by the nut manufacturer must be followed.
Holding the bearing using an Allen key
|
![]() |
Stud type track rollers with eccentric collar
Highest point on the eccentric collar
The highest point on the eccentric collar is indicated on the roller stud side, which also gives the position of the radial lubrication hole.
Commissioning and relubrication
Position of the relubrication holes
Stud type track rollers have a lubrication hole for relubrication:
- on the flange side of the roller stud
- on the thread-side end face for outside diameters from 22 mm
- on the shank of the roller stud, for outside diameters from 30 mm with an additional lubrication groove
Stud type track rollers with an eccentric collar cannot be relubricated via the stud. The eccentric collar covers the lubrication hole.
For lubrication, only grease guns with needle point nozzles may be used that have an opening angle ≦ 60° ➤ Figure.
Before commissioning, the lubrication holes and feed pipes must be filled with grease in order to ensure protection against corrosion; lubrication can be carried out at the same time.
Lubrication will be more difficult if a rolling element is located over the radial lubrication hole. Relubrication should therefore be carried out with the bearing still warm from operation and rotating if safe to do so, before the bearing comes to rest if safe to do so and before extended breaks in operation.
The grease used for relubrication should be the same as that used for initial greasing. If this is not possible, the miscibility and compatibility of the greases must be checked. Relubrication should continue until a fresh collar of grease appears at the seal gaps. The old grease must be able to leave the bearing unhindered.
Relubrication using a grease gun
|
![]() |
Schaeffler Mounting Handbook
Rolling bearings must be handled with great care
Rolling bearings are well-proven precision machine elements for the design of economical and reliable bearing arrangements, which offer high operational security. In order that these products can function correctly and achieve the envisaged operating life without detrimental effect, they must be handled with care.
The Schaeffler Mounting Handbook MH 1 gives comprehensive information about the correct storage, mounting, dismounting and maintenance of rotary rolling bearings http://www.schaeffler.de/std/1B68. It also provides information which should be observed by the designer, in relation to the mounting, dismounting and maintenance of bearings, in the original design of the bearing position. This book is available from Schaeffler on request.
Legal notice regarding data freshness
The further development of products may also result in technical changes to catalogue products
Of central interest to Schaeffler is the further development and optimisation of its products and the satisfaction of its customers. In order that you, as the customer, can keep yourself optimally informed about the progress that is being made here and with regard to the current technical status of the products, we publish any product changes which differ from the printed version in our electronic product catalogue.
We therefore reserve the right to make changes to the data and illustrations in this catalogue. This catalogue reflects the status at the time of printing. More recent publications released by us (as printed or digital media) will automatically precede this catalogue if they involve the same subject. Therefore, please always use our electronic product catalogue to check whether more up-to-date information or modification notices exist for your desired product.
Further information
In addition to the data in this chapter, the following chapters in Technical principles must also be observed in the design of bearing arrangements: