Friction and increases in temperature
Friction and wear
Friction describe the force that acts in opposition to motion. The key value stated is the coefficient of friction μ.
Friction is essentially dependent on the following influencing factors:
- the sliding contact surface
- the load
- the sliding velocity
- the bearing temperature
- the lubrication condition
- the quality of the sliding surfaces.
Fundamental curve of the coefficient of friction
For maintenance-free plain bearings based on PTFE, the fundamental curve of the coefficient of friction μ is shown as a function of sliding velocity, load and temperature, ➤ Figure. The coefficient of friction decreases with an increasing specific bearing load p and a decreasing sliding velocity v.
Coefficient of friction, fundamental curve
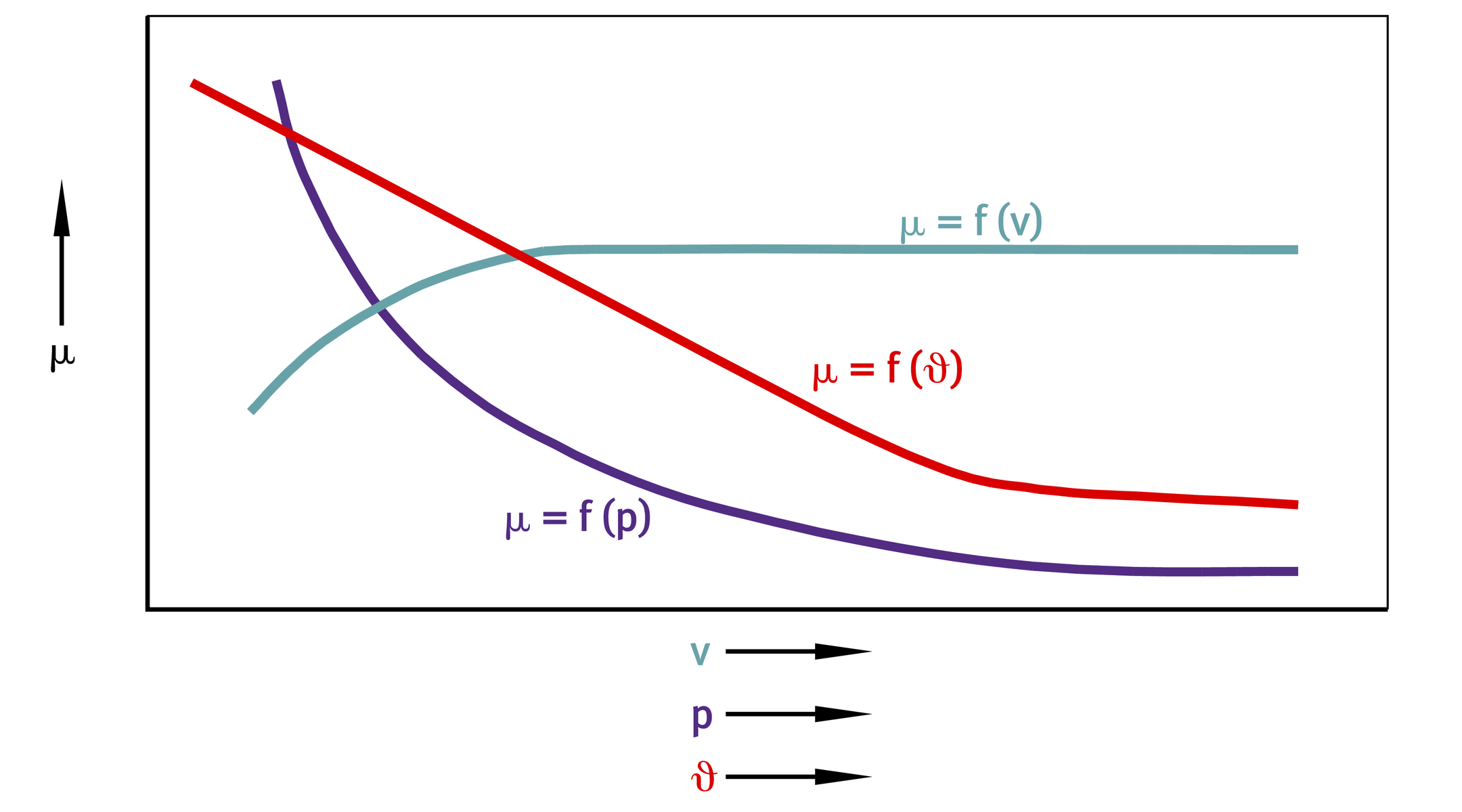
Friction and wear curve
The wear curve for maintenance-free plain bearings is divided into the running-in phase, main wear phase and failure phase, ➤ Figure. The main wear phase is approximately linear in character.
The friction curve of maintenance-free plain bearings shows a characteristic pattern in the three phases, ➤ Figure.
Friction and wear curve
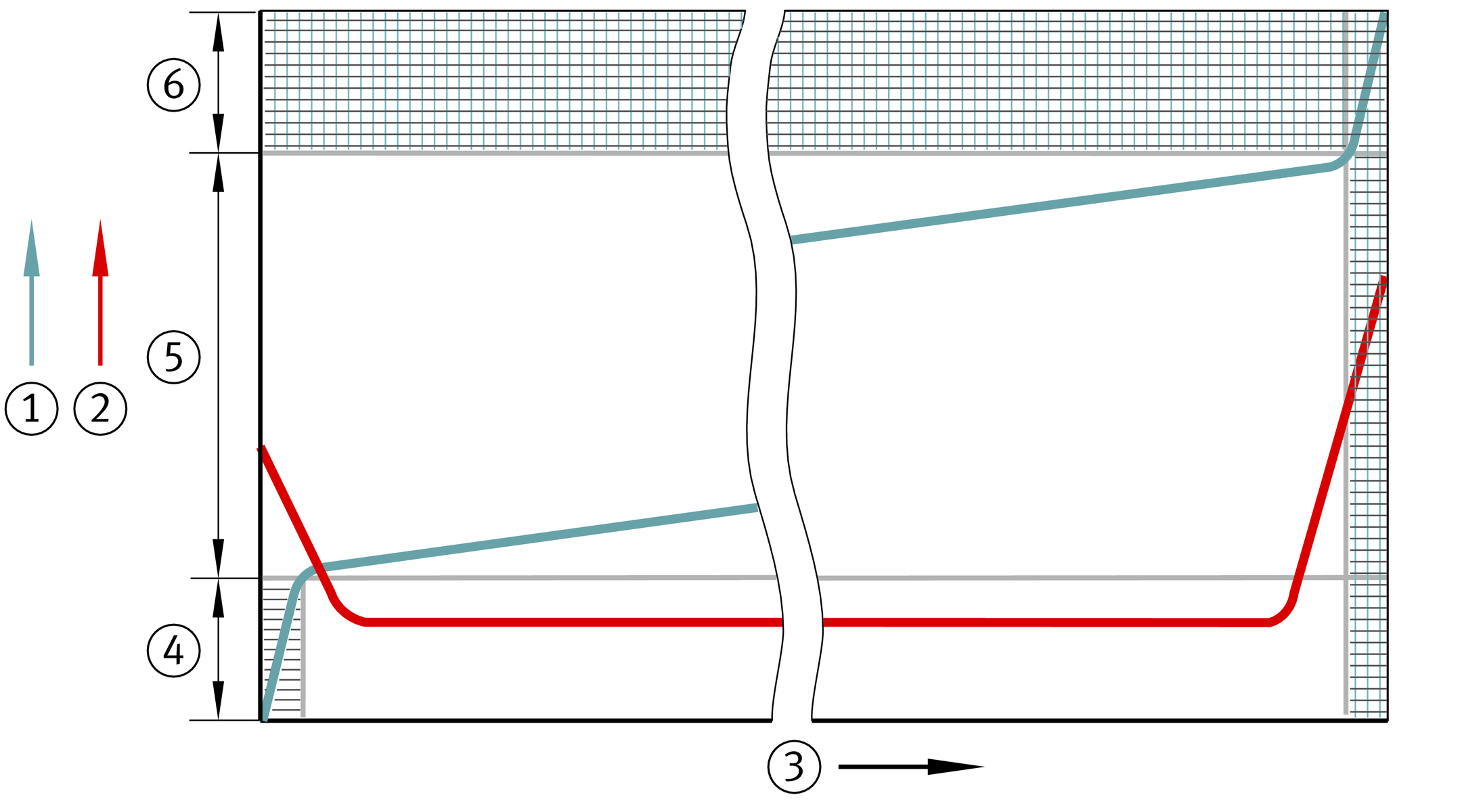






Bearing frictional torque
The bearing frictional torque M is valid under radial load in the case of radial and angular contact spherical plain bearings and in the case of bushes. In the case of axial spherical plain bearings and thrust washers, it is valid under axial load.
In the case of new plain bearings, the bearing frictional torque may be significantly higher during the early running-in phase. This is for the following reasons:
- Plastic transfer of the PTFE material occurs to the surface structure of the mating surface.
- The internal tribology of the bearing is not yet complete and PTFE particles are deposited on the mating surface and functional surface (PTFE/PTFE friction).
ACHTUNG
If spherical plain bearings are subjected to combined radial and axial load, the bearing frictional torque is determined by integration of the normal forces. In the case of flanged bushes, the frictional torque must be calculated for both the radial sliding surface and the axial sliding surface on the flange.
The information on coefficients of friction is valid for plain bearings without seals 2RS, 2TS, 2RS2 or 2RS4. For plain bearings with seals, the frictional torque of the bearing increases enormously as a function of the seal design.
Calculation
The bearing frictional torque M is determined as follows: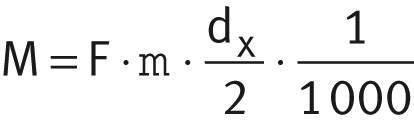
M | Nm | Bearing frictional torque |
F | N | Concentric radial or axial load |
μ | – | Coefficient of friction, see table |
dx | mm | Specific diameter, see table. |
ACHTUNG
For reasons of safety, the maximum coefficient of friction must always be used when calculating the drive power, see table. If the coefficient of friction is above the maximum value, this may lead to increased wear, a rise in bearing temperature and impaired functioning of the plain bearing.
Specific diameter
Plain bearing | Specific diameter dx |
---|---|
Radial spherical plain bearing | dK |
Axial spherical plain bearing | 0,7 · dK |
Angular contact spherical plain bearing | 0,9 · dK |
Bush | Di |
Flanged bush (radial sliding surface) | Di |
Flanged bush (axial sliding surface) | Dfl |
Thrust washer | Do |
Comparison of coefficients of friction
Sliding layer, | Mating surface | Coefficient of friction μ | |
---|---|---|---|
min. | max. | ||
E40** | Steel | 0,03 | 0,25 |
E50 | Steel | 0,02 | 0,2 |
ELGOGLIDE | Hard chromium coating | 0,02 | 0,2 |
ELGOGLIDE-W11 | Hard chromium coating | 0,02 | 0,15 |
ELGOTEX | Steel | 0,03 | 0,2 |
PTFE composite | Hard chromium coating | 0,05 | 0,2 |
PTFE film | Steel | 0,05 | 0,2 |
Steel/steel | 0,08 | 0,22 | |
Steel/bronze | 0,1 | 0,25 |
**For E40, detailed coefficients of friction must be observed.
Heat dissipation
Friction is converted into heat. Adequate heat dissipation is essential for the function of a plain bearing. This occurs through convection via the housings and shafts to the environment. In some cases, heat is carried away by means of the lubricant.
In plain bearings where high frictional energy pv is converted, increased heat dissipation is required.