Condition Monitoring
Features
The malfunction-free and optimised operation of complex machinery and plant can only be achieved by means of condition-based maintenance. Schaeffler uses vibration diagnosis as a preferred method here.
This method makes it possible to detect damage in machinery at a very early stage. This means that, for example, damaged components can be replaced as part of planned downtime. Unscheduled downtime is avoided.
Depending on the type of machine and its importance for the production process, condition monitoring can be carried out by means of either continuous (online) monitoring or regular (offline) monitoring.
Continuous monitoring
For production-critical machinery, continuous monitoring, ➤ Figure, by means of vibration diagnosis is indispensable in many cases.
In addition to giving advice on selecting the right system, Schaeffler also implements monitoring of the machine. This includes not only hardware selection but also system configuration and, where necessary, its integration into existing systems.
The customer can decide whether to carry out plant monitoring himself or to enlist the services of Schaeffler for online monitoring. Due to the communication options of the monitoring systems, remote analysis can be carried out by the Schaeffler experts.
Continuous monitoring
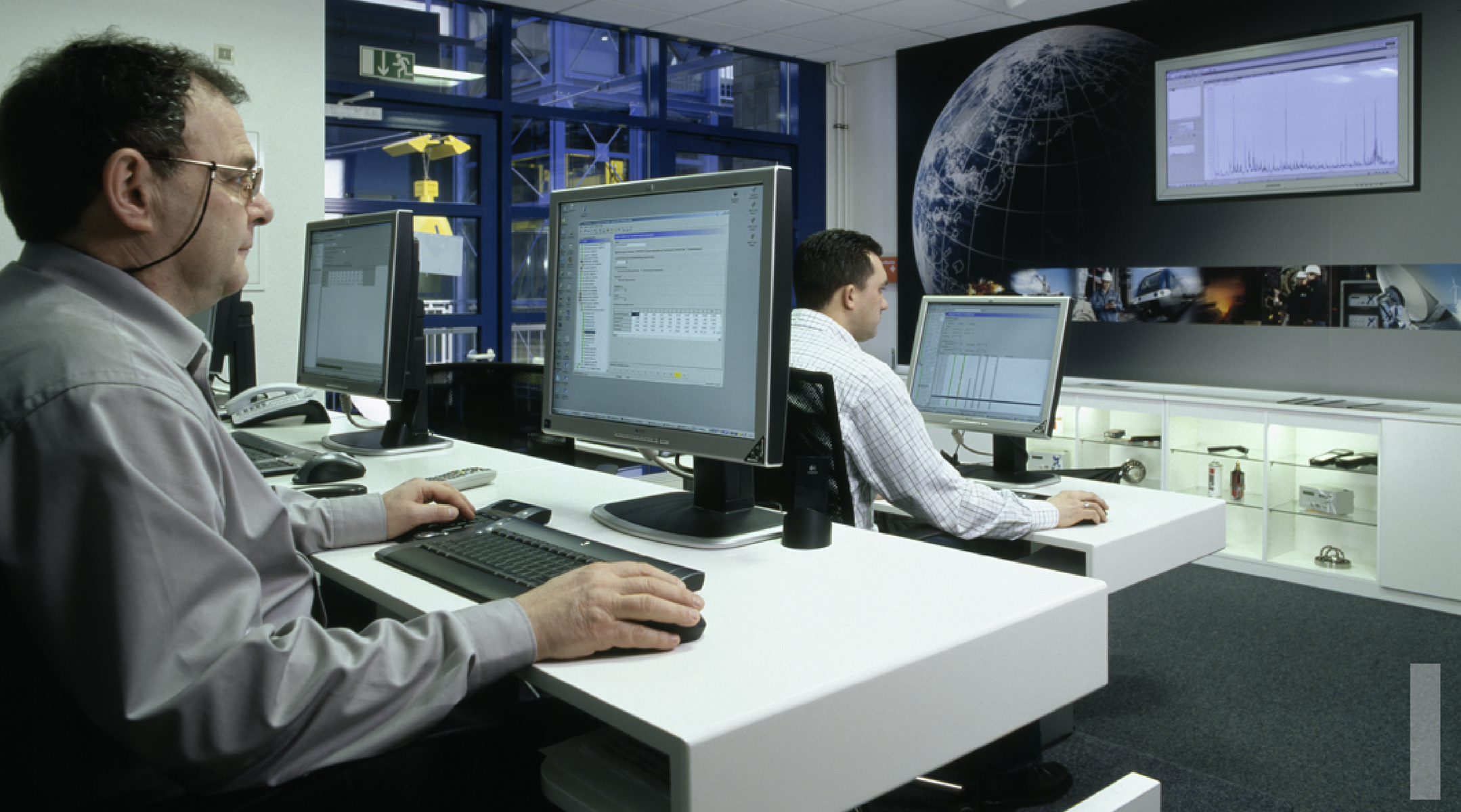
Regular monitoring
The failure of so-called “B” or “C” category plant items not does lead directly to downtime and does not therefore lead to expensive secondary damage. In the case of such machine parts, regular monitoring is generally recommended as a more economical option.
In this type of monitoring, machinery is examined and assessed by vibration analysis at regular intervals, for example every four weeks. This regularity gives more in-depth knowledge of the normal condition of the machine. Deviations can thus be detected. For the monitoring concept, the selection of measurement points and monitoring accessories as well as the measurement interval play a decisive role. If deviations occur during measurement or if trends are to be investigated, the data can be sent to the Schaeffler Diagnosis Centre. Vibration experts will then analyse the data and prepare a diagnosis report. Through working with the Schaeffler experts, customers can build up their own know-how in analysis.
If no personnel are available for data logging, Schaeffler can also offer support in data logging. The Company’s experts can carry out regular measurements on site.
Troubleshooting
Where malfunctions occur on a machine, defects must be detected and rectified very quickly. Based on many years of experience with different sectors and applications, the Schaeffler diagnosis experts are well versed in such troubleshooting tasks.
Problems or malfunctions in machine operation often become apparent through changes in vibration behaviour, unusual temperature patterns or similar phenomena. The investigation is closedout by a handover discussion between the diagnosis experts and all relevant employees on site. In addition to the results of the investigation, the recommended countermeasures are discussed in particular.
Further information
Enquiries: industrial-services@schaeffler.com,
+49 2407 9149-66..
Wear measurement system
In order to facilitate condition monitoring for plain bearings as well, Schaeffler has developed a special measurement method.
Several sensors distributed around the circumference allow continuous monitoring of the wear state and the temperature in the bearing, ➤ Figure.
In order to measure the depth of wear on a sliding layer in a maintenance-free spherical plain bearing, inductive sensors can be used. The data can be used, for example, to assist in calculating when the sliding layer will come to the end of its life. As a result, service intervals can be planned for reconditioning of the bearing.
The wear measurement system is available by agreement for large spherical plain bearings. These special bearings must be matched and calibrated specifically to the relevant application. In this case, please consult the Schaeffler engineering service.
Spherical plain bearing with wear measurement system
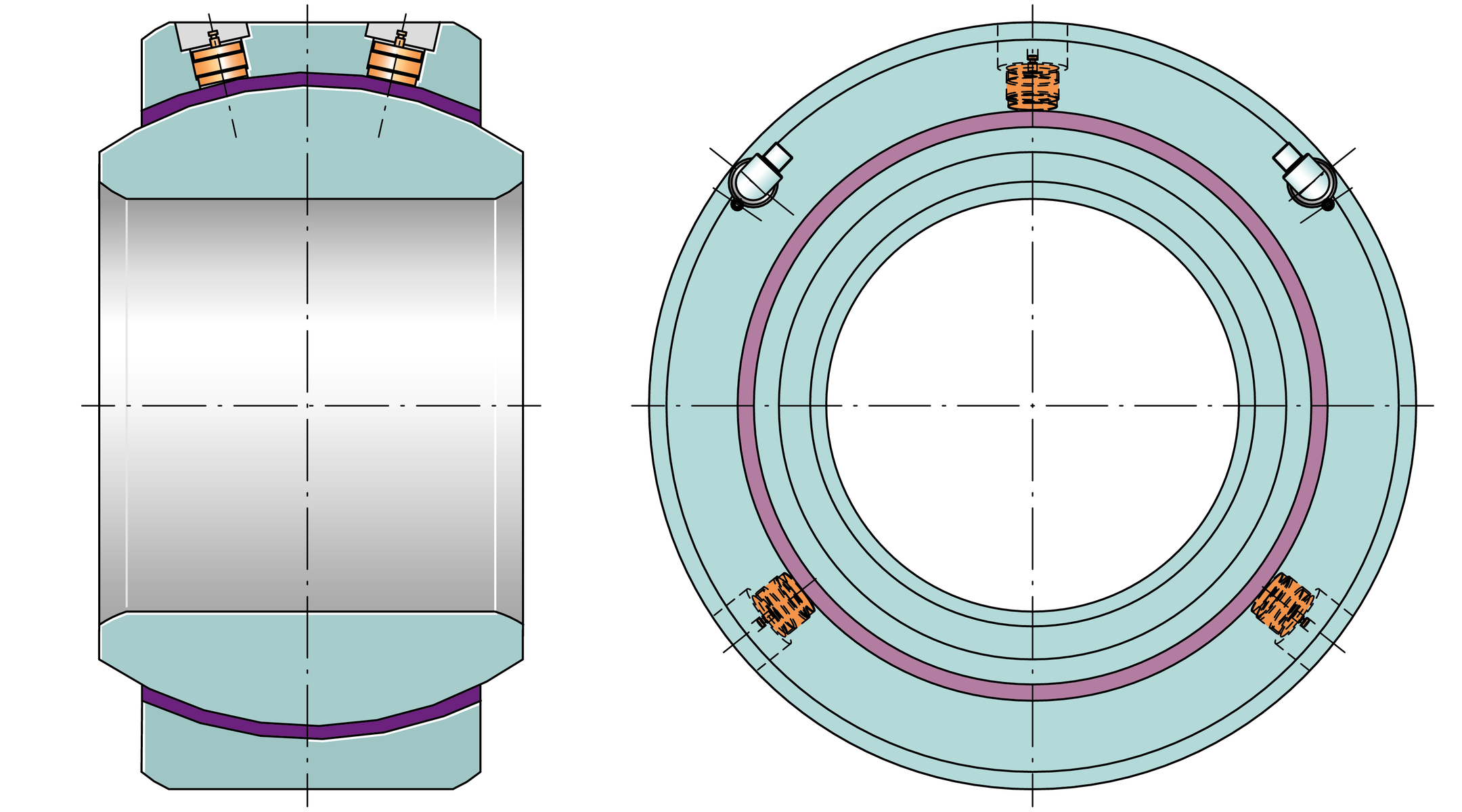